Among the nascent battery technologies with disruptive potential is sodium-ion (Na-ion), particularly in the rapidly growing energy storage sector. Recent developments are making the case for their use in entry-level cars too.
Chinese heavyweights like CATL and BYD have made a move towards the technology, while European players, like Stellantis and Northvolt, are now also entering the fray. A Volkswagen-JAC Chinese JV was the first to place a Na-ion battery in an EV late last year.
Na-ion batteries are a cheaper alternative to lithium-ion batteries as they are made from materials that are low-cost and abundant. Sodium is nearly 400 times more abundant than lithium. The costs per kilowatt hour of energy content is at least 20% cheaper than their dominant Li-ion counterparts—NCM and LFP.
.PNG)
Thermal stability is another benefit as sodium-ion cells work better at both very high and low temperatures. Northvolt said its Na-ion batteries would be able to withstand up to three times as much heat exposure as its lithium counterparts.
But their lower energy density relative to their size has long lagged behind Li-ion batteries, making sodium cells impractical for most EVs where space is at a premium. Na-ion batteries offer energy density of around 160Wh/kg, compared with 200Wh/kg for LFP batteries or 300Wh/kg or more for NCM.
While this low energy density, combined with a lower life cycle, will keep Na-ion batteries primarily suited for energy storage or two/three-wheelers, they are also expected to gradually cater to small, low-cost cars.
The success of Na-ion batteries will depend on prices of Li-ion batteries. Low lithium prices have made the cost-benefit less evident over the past year and is likely to delay some investments. We expect average Li-ion battery pack prices to decrease to US$115/kWh in 2025, from US$140/kWh last year.
How quickly manufacturers could scale up the new technology is another key factor. The cell manufacturing process for Na-ion cells is also almost identical to that of Li-ion cells. This means heavy investments would not be required to make the switch, which bodes well for the technology.
In the medium-term, we expect the use of Na-ion in light-vehicles to be modest at around 4% in 2030. The proportion will be higher in China, at around 6%, compared to 2% in Europe. For energy storage, the proportion will be higher at around 10% by then.
What’s the Difference?
The development of Na-ion batteries started in the 1990s and are now at a critical moment of commercialisation. One big advantage lies in the cost of sodium. Sodium carbonate costs around US$290t versus around US$15,000/t for lithium carbonate.
While the Na-ion batteries never use lithium, the need for other minerals—such as nickel and manganese—depends on the cathode chemistry. Further R&D efforts are being undertaken to find the ideal anode/cathode active material that allows scalability.
The majority of cell producers planning Na-ion battery capacity will be using layered metal oxide cathode technology, which promises higher energy density.
Northvolt and CATL use Prussian white, which is abundant and cheap, but has lower energy density. Another option is polyanion, used by France’s Tiamet, which is more stable but features toxic vanadium.
Similar to Li-ion cells, Na-ion battery cells have positive and negative electrodes, a separator, and an electrolyte. Both battery types involve positive ions traveling back and forth between the two electrodes during charging and discharging.
Similarly to LFP, Na-ion batteries were initially developed in the US and Europe, but China’s announced manufacturing capacity is around 10 times higher than the rest of the world combined.
Chinese Players
CATL launched its first generation of sodium-ion batteries, with an energy density of 160Wh/kg, in 2021. But that battery used a mix of sodium and lithium-ion cells. CATL is now aiming for a 200Wh/kg second-generation, exclusively sodium-based battery. CATL announced in April that Chery’s iCAR brand would use its sodium-ion batteries, alongside lithium-ion.
CATL’s rival BYD is also actively pursuing sodium battery technology. At the end of 2023, BYD and tricycle giant Huaihai signed a CNY10bn (US$1.4bn) contract to build a 30GWh plant for sodium-ion batteries in Xuzhou, Jiangsu province. BYD’s US$11k Seagull hatchback will be its first EV to use sodium-ion batteries.
Yiwei, jointly owned by Volkswagen and JAC, started producing its first EVs with Na-ion batteries from Hina in late 2023. The new EV, known as E1OX, has a sodium pack with a capacity of 25kWh, an energy density of 120Wh/kg, and a range of 250km. Around 5k of them were exported to South America in February. Xia Shunli,
Chairman of Yiwei, said Na-ion batteries will become “complementary to LFP batteries”. Hina’s batteries use a Na-Fe-Mn-Cu based oxide cathode and an anthracite-based carbon anode. Hina commissioned a 1GWh Na-ion production line in 2022.
Western Players
Northvolt validated a 160Wh/kg sodium-ion battery in November. That puts it further ahead than CATL, which used metal oxides in its sodium-ion cells. Northvolt’s version used Prussian blue, a pigment first used in the 18th century to make blue paint.
The Swedish company is Europe’s current biggest hope to compete against the dominant Asian battery producers. The possibility of reducing dependency on China for processed raw materials is a key incentive for Western firms to consider Na-ion. China accounts for around 70% of global Li-ion battery production.
Na-ion batteries “are not that dependent on a number of these strategic supply chains that China has created in a very efficient way,” said Peter Carlsson, Northvolt’s chief executive and co-founder.
Carlsson expects orders for energy storage batteries in 10 years could be “as big or potentially bigger than the current portfolio” for EV batteries, which currently stands at US$55bn. Carlsson said he thought Na-ion batteries would be about 25% cheaper than the Li-ion batteries typically used in energy storage. Northvolt is hoping to provide the first samples to customers this year and reach full-scale production by 2030.
Smaller players are also doing their bit to bring Na-ion technology to commercialisation. UK-based Faradion, which was acquired by Indian conglomerate Reliance Industries in 2021, is aiming to have a megawatt capacity for Na-ion batteries by 2025 and then scale up to gigawatt scale. The company’s first-generation cells have an energy density of 160Wh/kg.
Tiamat plans to soon start construction of a 5GWh plant in France. First-phase capacity of 0.7GWh is targeted by the end of 2025. The plant will create 1,000 jobs. Before expanding to EVs, it will initially focus on power tools and stationary storage. The company raised EUR30m in in January. Similar financing is planned the coming months, bringing total investment to around EUR150m. Stellantis is a key investor.
The US is also making moves. In January, Ohio-based Acculon Energy announced series production of its Na-ion batteries for energy storage. It aims to scale production to 2GWh by mid-year. Natron Energy, a spinoff out of Stanford University, started series production last month at its 600MW plant in Michigan. Meanwhile, Colorado-based Peak Energy raised US$10m in seed funding in October. The company said it will initially Na-ion import battery cells from China.
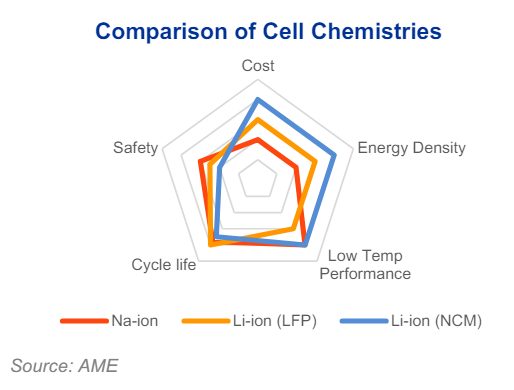
Companies investing in Na-ion batteries are bullish on the technology’s combination of thermal capability, cost, and sustainability. With manufacturers claiming that their next-generation sodium-ion batteries will have the same energy density as LFP at 200Wh/kg, sodium-ion batteries will start making a lot more sense for use in cars. Furthermore, as public charging networks are built up, long-range batteries will become less of a priority, boosting the attractiveness for cheaper EVs, that could be powered by Na-ion batteries.